

Once flooded, the aluminum-based neutron absorber materials used in most DPCs would readily degrade. However, some small number of disposal overpacks could fail within the postclosure performance period due to corrosion or disruptive events. Without flooding of waste packages with ground water, criticality can never occur. If backfill is used around DPC-based packages its peak temperature could be 150 to 200 deg.C. Sedimentary media such as shales pose special challenges especially if they have low thermal conductivity. For disposal in salt, DPC-based waste packages could be emplaced at only 50 to 100 years from discharge, depending on burnup. Calculations for emplacement in hard rock and sedimentary rock show that host rock peak temperature targets of 100 to 200 deg.C could be met by managing fuel age and burnup, with repository closure at up to 150 years from reactor discharge. In general DPC direct disposal would cost tens of billions of dollars less, in packaging and disposal costs. The cost of DPC direct disposal in various geologic settings has been compared to options involving a change to loading standardized multi-purpose canisters, or continuing to load DPCs and re-packaging all of them for disposal. Engineered solutions are available for transporting and emplacing them underground, although some could be the largest of their kind. Earlier studies showed that DPC-based waste packages would be only slightly larger and heavier than those proposed for a repository in volcanic tuff. Containment functions would be assigned to the disposal overpack, and published data show that suitable materials exist for most possible disposal environments. The postclosure safety case for DPC direct disposal would resemble that for any repository-waste isolation would be enhanced by choosing host geology in which radionuclide transport is diffusion dominated, and for which more » transport properties and pathways are insensitive to the expected temperature history. Technical objectives for disposal are: 1) safety of workers and the public, 2) engineering feasibility 3) thermal management and 4) criticality control after permanent closure of a repository. = ,ĭirect disposal of commercial spent nuclear fuel (SNF) in dual-purpose canisters (DPCs) could avoid the cost and complexity of re-packaging spent fuel into smaller purpose-built containers, avoid disposing of the DPC hulls as low-level waste, and potentially decrease worker dose. The motivation for this work is to better understand the potential for periodic criticality events, cannister damage, and release of radionuclides during a criticality event in a DPC. It is important to understand the change in hydraulic transmissivity between the canister and surroundings for two reasons: first, because it may control the more » potential for and frequency of subsequent criticality events second, because it will control the release of radionuclides from the canister. This internal pressurization may cause the initial fractures in the canister and overpack to grow. Such an event would release enough energy to boil the water between the fuel rods and pressurize the cannister. Fresh water is a neutron moderator thus, if the canister internals and fuel assemblies have been sufficiently degraded, a criticality event could occur.
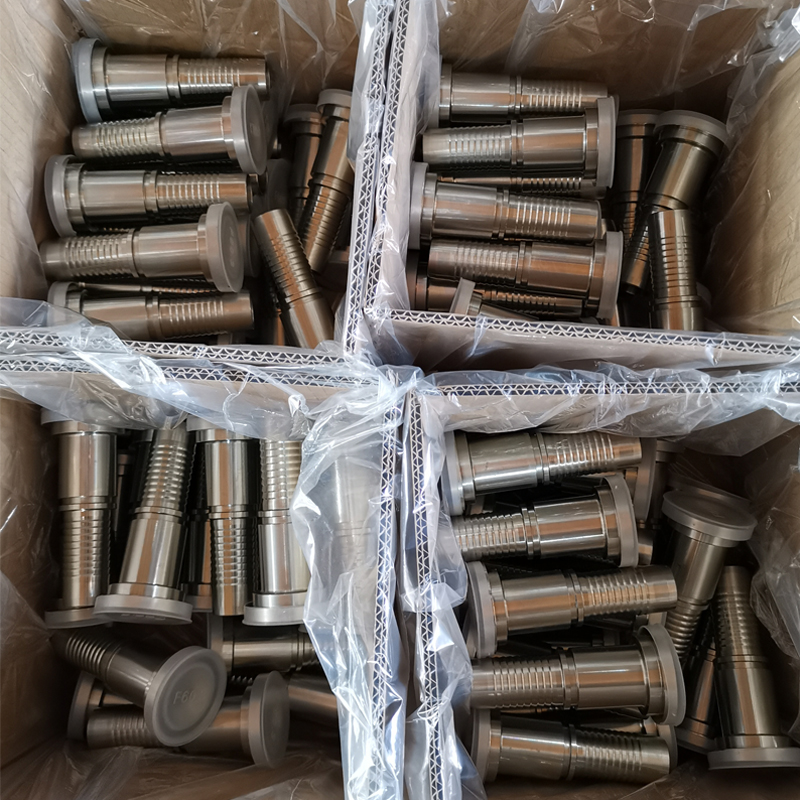
A breach in the canister could allow groundwater to fill the canister. Over geological timescales, it is envisioned that the canister and canister overpack will develop fractures due to stress corrosion processes. Post closure criticality control is an important aspect of this investigation. Department of Energy Office of Spent Fuel and Waste Science & Technology is investigating the performance of DPCs for direct geological disposal of spent nuclear fuel. The work is being done to enable a coupled mechanical-thermal-hydraulic analysis of a potential criticality event in a dual purpose cannister (DPC). Sandia National Laboratories has hired Itasca Consulting Group, Inc., the authors of the FLAC3D geomechanics software, to couple FLAC3D with TOUGH3, the porous media flow solver.
